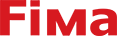
The integrated and automated staff and vehicle access control and time & attendance registration system introduced in Lithuania’s largest fertiliser plant ensures time & attendance registration for 1,000 employees, access control for visitors and generates reports according to a number of metrics.
FIMA and its partner, a software solutions developer, have introduced an integrated and automated staff and vehicle access control and time & attendance registration system in the Lifosa plant in Kėdainiai which is owned by Eurohem, one of the world’s largest producer of mineral fertilisers.
Previously, the company used three separate systems for access control for people and vehicles and time & attendance registration. These were not integrated and automatic data exchange between them was impossible. The aim of the project was to integrate Lifosa’s systems into a single system and to improve the efficiency of process management.
As part of the integrated system concept, video surveillance, access control, registration plate recognition and time & attendance registration systems were introduced and integrated with existing HR, registration and logistics systems. Special software was tailored to the plant’s needs to enable control of the systems via a single interface.
In addition to reducing the amount of administrative work, eliminating overlapping tasks and ensuring efficient and easy access control for more than 1,000 employees and visitors, time & attendance records and other processes, the solution introduced by FIMA and its partner has improved safety for everybody on site.
The integrated system at Lifosa now enables:
The project included unique integration between HR management, time & attendance, logistics, surveillance and access control systems.
“We were looking for a system integrator able to tailor basic software to our needs and to ensure its integration with the terminal equipment made by different manufacturers.”